Gettin’ Tight, Truly
Okay, now you’ve got a wheel that’s true, but you’ve still got to tighten all its spokes to make it strong. Doing so could very easily undo all your careful work up to this point, unless you’re extremely careful and patient. If your patience is wearing thin, this is a good time to take a break. Come back to the job when you can focus comfortably for another stretch of time.
Choose a unique spot on the rim, such as the valve stem hole, and decide on a direction to rotate the wheel. Call the first spoke you come to number one, the next number two, etc. until you’ve come to the end of the repeating pattern of spokes in your wheel. In the vast majority of cases, this will be a total of four spokes, as mentioned earlier, so that’s what we’ll use for our example here. Tighten spoke number one a small amount, such as a half-turn. Count three spokes in your chosen direction of rotation. Now tighten this spoke, which will be spoke number four in the first series, the same amount you tightened number one. Now count three more spokes. This will be spoke number three in the second series. Tighten it the same amount you tightened the others. Count three more spokes. This will be spoke number two in the third series. Tighten it the same amount.
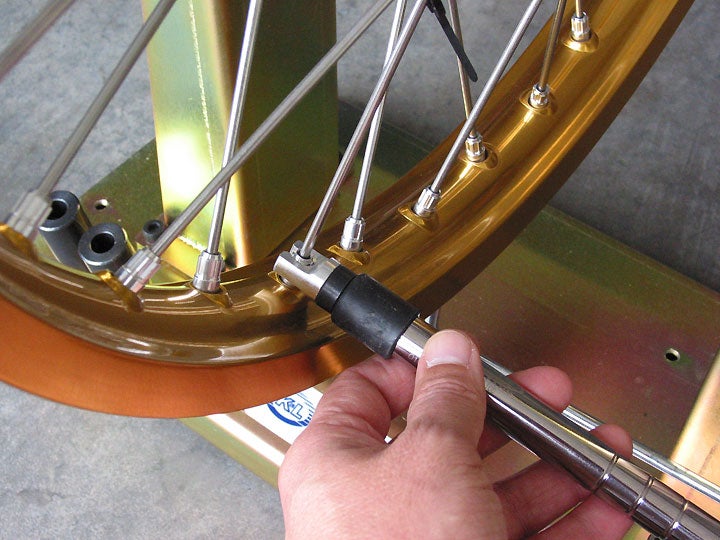
Keep doing every third spoke until you’ve gone all the way around the wheel three times. Keep track of that place-keeper you chose at the beginning, and advance your starting point one spoke at the conclusion of each revolution. If you look closely, you’ll see that this method distributes the impact of your efforts as evenly as possible across all four types of spokes–left, right, inner, and outer. This minimizes the induction of distortion in any particular direction, averaging out any errors that get produced along with way.
Time to check runout again. Correct any unacceptable deviations by the same methods outlined earlier, doing north-south adjustments first and then managing whatever left-right problems still remain. When the wheel is once again true in both dimensions, perform another round of tightening using the every-third-spoke method. Then recheck runout and adjust as necessary. Continue to repeat these steps until all the spokes are tight enough, with the wheel remaining true.
Enough is Enough!
But how tight is “tight enough”?! Well, for those who don’t mind spending big bucks for high-tech precision, there are actually a few torque wrenches on the market made specifically for spoke nipples. If you’re so equipped, you have a mechanical standard you can make every spoke meet. If you don’t want to invest in such garage exotica, you can check your spokes the old-fashioned way–by ear. Just as a guitar or piano string produces a higher pitch when pulled tighter (and struck), a spoke’s tension will be revealed in the sound it makes when tapped by another metallic object. Spokes with inadequate tension will make a relatively lower-pitched, short-lived note, while those with adequate tension will create a relatively higher-pitched ring of longer duration. It’s not necessary for all the spokes to emit exactly the same sound. But they should all ping instead of twang. There is a distinct difference between the two tonal ranges; variations within either range are irrelevant. Simply tap your spokes as you tighten them, and listen for the shift in tone.
What if a correction needs to be made in the direction of spokes that are already plenty tight? Remember that each spoke pulls against two sets of opposing spokes–those on the opposite side of the wheel north-south, and those on the opposite side of the rim left-right. In many cases, corrections can be made not only by tightening spokes according to the steps outlined above, but also by loosening the opposing spokes. Once well-familiarized with this process, you may make corrections by doing a tiny bit of both, keeping all spokes involved within the optimal range of tension.
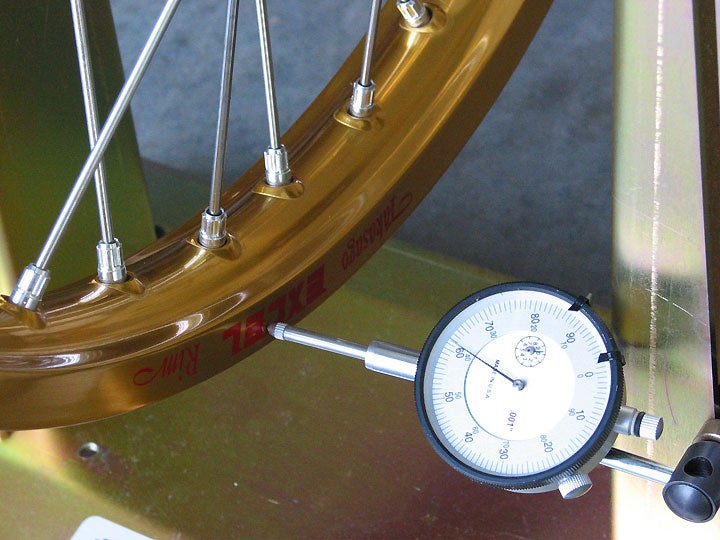
So how true is really true enough? Well, first consider the entire wheel as a system. The tire flexes tremendously when compared to the rim, and will obscure, and compensate for, minor irregularities in the rim’s roundness; the larger the tire, the more this is the case. (The tire adds its own irregularities of shape to the mix, too, which are inconsequential unless extreme.) The precision of a wheel’s shape, just like its state of weight balance, becomes more important with increasing speed. So relatively slow moving dirt bikes, which are simultaneously dealing with huge irregularities in ground surface, can actually tolerate quite a bit of wheel shape error; a stiff wire used as a truing armature will provide adequate precision. But what about a high speed street bike?
With all spokes tight and your rim running true throughout its full revolution, your naked wheel is ready for tire mounting, unless you notice any spokes sticking out beyond the outside edge of their nipples. Carefully grind any protruders down so they pose no threat to your delicate innertube.
And that pretty much sums it up! But just remember that spokes can loosen over time. Although there are conflicting opinions about whether or not a correctly assembled/torqued wheel actually “settles in” (soon requiring some touch-up retorquing of the spokes), don’t be surprised if your brand new bike’s wheels fail inspection right off the showroom floor. We’ve found some very loose spokes on factory fresh machinery. And any loose spokes make it easier for other spokes to come loose on the opposite side (north-south and left-right), increasing the potential for wheel failure; that’s a bad thing. So check spoke tension regularly, especially after riding over rough surfaces or hitting a large bump. And set aside the time to inspect runout once in a while; it’s easiest to do at tire-change time, if you change your own tires. You may discover that proper spoke maintenance solves an elusive vibration problem. It will certainly help prevent wheel failure, just as keeping your tires properly inflated makes them better able to handle the stresses to which they’re subjected.
Spoke wheels can be things of great strength and beauty, but keeping them that way requires occasional painstaking attention. Proceeding slowly and carefully through the procedures in this article will yield a true wheel in the shortest possible time. Rushing and carelessness will turn a boring chore into a nightmare of oscillating errors, and produce a disfigured rim that could be diagnosed with a quick glance from ten yards away. And then you’d have to start over and do it all again slowly anyway. It’s your choice.